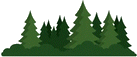
1992 Memorandum
Mechanization, Technological Change and Automation
The following language is the memorandum of agreement that was signed on February 11, 1992. Some interpretive comments have been added near the end of the document as key points of understanding for the knowledgeable application of the memorandum.
Memorandum of Agreement
Where the result of Mechanization, Technological Change and Automation new jobs are created or existing jobs are significantly changed and where the existing benchmarks no longer fit such jobs, the following criteria will apply in establishing the appropriate Group ranking. In the application of these new criteria those categories will also be considered where the result of Mechanization, Technological Change and Automation the position is responsible for additional processing equipment, e.g. Canter with multiple Gangsaws; Edger with Circular Gangsaw; Twin Gangsaws. The new criteria would not apply where the equipment is presently covered by existing criteria.
Where Optimization of a unit is such that the position requires constant monitoring and manual override, the category will be placed in the same group as the comparable conventional job category.
- Group 14 - Main Edger - Conventional
- Group 14 - Main Edger - Optimizer Assist
Where Optimization of a unit is such that the position requires constant monitoring only, or the Operator may occasionally operate the unit manually for normal production purposes, the category will be placed proportionately lower than the comparable conventional job category.
- Group 9 - Gang Edger - Conventional
- Group 7 - Gang Edger - Monitoring
In addition to the application of (1) and/or (2), the following criteria will be considered to establish the final Group for each category.
- Flow Responsibility – This measures the impact of the position on the inflow and outflow of the product.
- Inflow – One group is to be added for each additional separate inflow controlled by the operator.
- Outflow – One group is to be added for each additional separate outflow where the direction or presentation of the product is controlled by the operator.
- Product Recovery – This measures the primary responsibility of the position for maintaining or increasing recovery and grade relative to the additional piece (s) of equipment.
- Machine Centers – This measures the number of pieces of equipment controlled by the position. One Group is to be added for each additional machine center controlled by the Operator.
Note:There will be no automatic pyramiding of credits under the above three criteria.
Key Points
This agreement deals specifically with processing machine centers only. Trim tables, dropsorters, and hulasaws etc. are not included.
Three things to consider regarding Mechanization, Technological Change and Automation:
- Has a new job been created?
- Has a job been significantly changed?
- Does the job no longer fit the benchmark job description?
Answering yes to any one of these questions means you should consider a rate revision under the criteria outlined in this agreement.
When analyzing flow responsibility, understand that every machine center has one inflow and one outflow already included in the benchmark category. When considering flow responsibility, the inflows and outflows must be separate and additional.
When considering inflows, product must come from a storage area and the storage area must be controlled by the machine center operator.
When considering product recovery, the operator must be increasing the recovery of the product that is being processed by the additional machine center.